Engineering Q & A
Here is a list of common questions related to engineering topics. If you do not see your question here,
use the contact portal and we will try our best to answer your
question as soon as possible.
Q: What is unique about industrial components and components used by manufacturing companies?
A: Oftentimes, industrial components and components used by manufacturing companies need to be very heavy duty, rugged and
durable. Tooling is often a good definition of the type of items and components used. For example, if an industrial
or manufacturing company is making multiple parts repeatedly, the components and deviced used to make the parts take on
a tremendous amount of stress and strain. The tool materials must be must harder and more rugged than the parts being made.
Diamond is employed to grind away the hardest of materials such as ceramic.
Q: How can a designer accomodate the unique needs of industrial and manufacturing applications?
A: As with any design, it is important to have as complete an understanding of the entire system as possible. Testing is
also required. Testing can be done with scale models, on computers and with real devices and components. It is important
to understand how the end-user will use the item in question. The testing will help determine the expected failure mechanisms.
Testing will also spell out how many cycles the items can endure and what type of deterioration, if any, is to be expected.
Cutting corners on industrial and manufacturing components is not usually a good idea because the components and devices need
to be long-lasting and extremely reliable. For example, if a component fails on a manufacturing line, it could cost millions
of dollars in lost production.
Q: What is the best way to reduce manufacturing production costs?
A: Design the item such that manufacturing costs are minimized. For example, a designer may order prototypes from a manufacturing
company and then discuss with the contract manufacturer potential ways to reduce costs in terms of minor dimensional and tolerance
changes. At times, major changes may be considered as well. Apple used to use a metal antenna but after a design review decided
that what was needed was a thin thermoplastic piece, rectangular and thin, with copper painted over it in a pattern. This is a good
design because the plastic acts as a good insulator and is inexpensive. Compared to the old design, the new design saves money and
weighs less. Weight alone is incredibly important due to many factors including product distribution.
Q: How long does it take to have industrial components made?
A: Times vary but for repeat orders the lead time can be just a day or two. For the first-time order, the lead time is usually a couple
of weeks or so.
Q: How can we shorten the lead time?
A: If you use common materials or supply the materials it might help with the lead time. For example, special exotic metals can take
a bit of time to acquire versus aluminium, steel, stainless, copper or Kovar. Titanium can take a bit longer as can platinum along with
plated parts. Hastelloy and high-temp alloys usually take 3 weeks or so for production. If you place a blanket order for scheduled
deliveries, we can have the material ready to go and can ship early on demand in most cases thereby reducting the effective lead time to
merely hours if located in Silicon Valley, or a few days if located around the world because we can ship immediately.
Q: What is a source for plating?
A: John at Prodigy Surface Tech. is an excellent source. We suggest you contact him with your plating needs. Another option is Gail McKee
at FHE (featherholloweng@gmail.com). Another source is Epner in Brooklyn, New York. All of these three sources do excellent work.
Q: Where do I go for chem film and anodizing?
A: One place to try is PK Plating in the Silicon Valley area.
Q: Is Alloy 42 a good option for industrial applications?
A:. Alloy 42 (also known as Pernifer 40, Nilo 42 and Glass Seal 42) consists mainly of iron with 42% nickel. This material is used to seal to glass. Electronic tubes, hermetic packages, automotive lamps and industrial lamps all use Alloy 42. For more
information on Alloy 42, send a text to (209) 425-1555.
Q: What kind of tank should I use for my plating and surface engineering needs?
A: It depends on your particular application but one common design features a 3/4" minimum thickness polypro tank with reinforcement.
Q: Why is a heater baffle needed for my plating tank?
A: Heater baffles are used primarily to maximize flow over heater and minimize bath agitation.
Q: Where should the pump outlet on a cleaning tank be located?
A: The pump outlet should be positioned to ensure flow over the heater in order to minimize local overheating and prolong solution life.
Q: How do I save water during my rinsing processes?
A: Use a cascade system. Cascade rinsing processes reduce H20 requirements by 90% compared to previous requirements. For more information including a free diagram, text a request to (209) 425-1555.
Q: What are refractory metals?
A: Refractory metals are the group of metals that have boiling points over 4000 deg C. They are found in the 5th and 6th periods in groups
IVB - VIIB in the periodic table. They are moly (molybdenum), tungsten, tantalum, niobium, rhenium, zirconium and hafnium. Titanium,
vanadium and chromium are sometimes considered refractory metals but they do not meet all of the qualifications. Those three pretenders
come very close but they cannot cut the mustard at very high temperatures like the true refractory metals can!!
Q: What grit size should be used when grinding pure molybdenum?
A: For plain surfacing and cutoff grinding, 60 grit is recommended.
Q: I'm working on some form surface grinding of pure molybdenum but am unsure what grit to use. Also, I need to know any other information you have on wheel
grading in terms of form surface grinding.
A: We recommend aluminum oxide with friable grain type. Grit size 100; Grade I; Structure 5; Bond Vitrified.
Q: What else can you tell me about form surface grinding of pure molybdenum?
A: For sharper radii, finer grit size may be needed. We recommend wheel speed 5500-6500 sq ft per minute; Table speed 50 F2M; Dry; .001 infeed per pass (inches);
Open wheel dressing; AA100-15-V40 dry carborundum grading
Q: We are doing some finishing work with a cylindrical CNC grinding machine. What specs would you recommend? If I run into any trouble, who do I text?
A: If you run into any trouble, text Gail @ FHE (209) 425-1555; Here are the recommended specs: 5500-6500 wheel speed sq ft per minute; Table speed 1/6 (width of
wheel per revolution of work); 120 sq ft per minute work speed; Oil/water emulsion griding fluid; .001 + sparkout infeed per pass (inches); Fine wheel dressing;
Aluminum oxide grain; Semi-Friable; 80 grit size; Grade K; Structure 6; Vitrified bond; Wet carborundum grading DA80-K6-V11.
Q: What can you tell me about corrosion resistance relating to molybdenum?
A: Molybdenum provides corrosion resistance that is similar to tungsten. Molybdenum particularly resists non-oxidizing mineral acids. It is relatively inert to
carbon dioxide, ammonia, and nitrogen to 1100 deg C and also in reducing atmospheres containing hydrogen sulfide.
Moldybdenum offers excellent resistance to corrosion by iodine vapor, bromine and chlorine, up to clearly defined temperature limits. It also provides good resistance
to several liquid metals including bismuth, lithium, potassium and sodium.
Q: What is TZM?
A: TZM (titanium, zirconium, molybdenum) is molybdenum's prime alloy. This alloy contains 99% Mo, 0.5% Ti and 0.08% Zr with a trace of carbon for carbide formations.
TZM offers twice the strength of pure moly at temperatures over 1300 deg C. The recrystallization temperature of TZM is approimately 250 deg C higher than
moly and it offers better weldability. The finer grain strcture of TZM and the formation of TiC and ZrC in the grain boundaries of the moly inhibit grain growth
and the related failure of the base metal as a result of fractures along the grain boundaries. This also gives TZM better properties for welding. TZM costs around
25% more than pure moly and is 5-10% more expensive to machine.
Q: What is TZM used for?
A: Some applications for TZM include rocket nozzles, furnace structural components and forging dies.
Q: We are working with molten zinc. What are our options for containment and handling?
A: Moly/30% Tungsten was developed for the zinc industry. Moly/30% Tungsten resists the corrosive effects of molten zinc.
Q: Why use molybdenum?
A: There is an increasing demand from the electronics and aerospace industries for materials that maintain reliability over ever-increasing temperature conditions.
Because molybdenum's material properties meet the requirements, molybdenum is used by industry.
-Moly is very strong and stiff at high temperatures
-Good thermal conductivity
-Low thermal expansion
-Low emissivity
-Low vapor pressure
-Electrical resistivity
-Corrosion resistance
-Purity
Here are some applications:
-Rocket nozzles
-Jet tabs
-High temperature dies
-Electrodes
-Boring bars
-Tools
-Brazing fixtures
-Electrical contacts
-Boats and crucibles
-Heat shields
-High vacuum applications
-Glass-to-Metal seals
-Many others
Q: What forms are molybdenum available in?
A: Wire, ribbon, foil, plate, sheet, rod, billet, slab, bar, extruded shapes, tubes and powder are the available forms of molybdenum.
Q: What are some things I need to know about when working with molybdenum?
A: Here is a tip or two:
-The cutting speed for moly is 50% higher than high strength steel and ~3X faster than nickel-base alloys.
-Apply copper shims at all chucking and workpiece contact points.
Q: How do I thread molybdenum material components?
A: Threading is usually performed by thread grinding, single point turning or chasing operations. Carbide tools should be used and best results are obtained
when a perfect setup is locked in. One starting point is:
-Back rake 10 deg
-Side rake 5 deg
-10 deg clearance on leading edge
-3 deg clearance on trailing edge
-Rough threading can be done at 70 to 125 feet per minute
Q: I am putting in a fine, shallow thread. Any recommendations?
A: Rather than turning, we recommend grinding. We do not recommend using a die for this particular application.
Q: What are some other properties of molybdenum?
A: Here are some physical properties (all @20 deg C):
-Atomic number: 42
-Atomic weight: 95.94
-Density: 10.22 g/cc
-Melting point: 2610 deg C
-CTE 4.9 * 10^-6/deg C
-Electical resistivity: 5.7 uohms-cm
-Electrical conductivity: 30% IACS
-Specific heat: 0.061 cal/g/deg C
-Thermal conductivity: 0.35 cal/cm^2/cm-deg C/sec
-Mdulus of elasticity: 46 x 10^6 psi
-Boiling point: 5560 deg C
Q: Do you have any information regarding molybdenum tensile strength in terms of temperature variations?
A: Yes, here is a reference chart.
Q: What is Alloy 20?
A: Alloy 20, also known as Carpenter 20 (in cast forms designated as CN7M) is used like 316L but especially is the application needs to deal with stress corrosion cracking. It is a Ni-Cr-Mo stainless steel alloy.
Q: What else can you tell me about Alloy 20?
A: Here is some more information:
Composition
Nickel, 32.5–35%
Chromium, 19–21%
Carbon, 0.06% maximum
Copper, 3–4%
Molybdenum, 2–3%
Manganese, 2% maximum
Silicon, 1% maximum
Niobium, (8.0 X C), 1% maximum
Iron, 31–44% (balance)
Other names
UNS N08020
DIN 2.4660.
CN7M
Carpenter 20 CB 3
AL 20
Carlson Alloy C20
Nickelvac 23
Nicrofer 3620 Nb
Specifications
ASTM B729, B464, B366, B463, B473, B462
ASME SB729, SB464, SB366, SB473, SB462
ANSI / ASTM A555-79
EN 2.4660
UNS N08020
Werkstoff 2.4660
Q: What are the specifications for Alloy 42?
A: Here are the specifications:
ASTM F-30
Mil 1-23011 CL5
AMS 1-23011 CL5
Q: Can Alloy 42 be used to seal metal to glass?
A: Yes, Glass Seal 42 is one of the names for Alloy 42.
Q: What are the other names of the product besides Alloy 42 and Glass Seal 42?
A: The other names are Pernifer 40 and Nilo 42.
Q: I see mpy listed as a corrosion metric. What is mpy?
A: Mpy is mils per year, i.e., .001 inch per year. For example, if the data is 40 mpy, that means under test conditions
the material tends to lose .040" per year from the surface due to corrosion and reaction between the given media and test
material.
Q: What is the C.T.E. for Alloy 42?
A: The C.T.E. of Alloy 42 is dependent on temperature. See Figure 10.
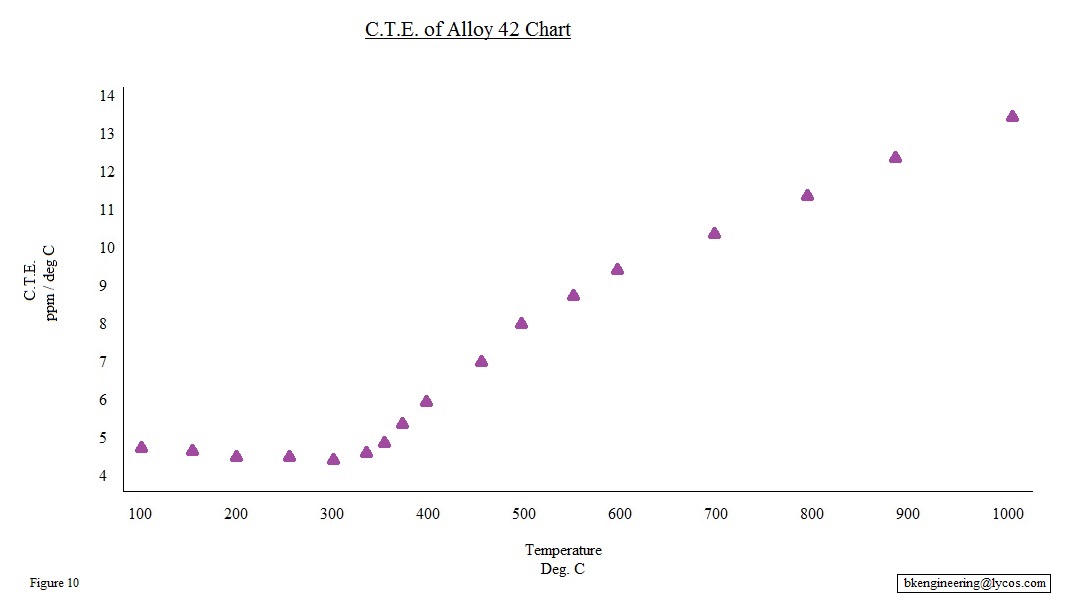
Q: What is Invar?
A: Invar, also known as Invar 36, Pernifer 36 and NILO 36 is a material used for precision instruments
and many applications utilizing Invar's low CTE at ambient temperatures.
Q: What is the CTE of Invar?
A: The CTE varies according to temperature. Here is a chart showing the range of CTE's for Invar vs.
temperature:
Q: What kinds of items are made of Invar or partially made of Invar?
A: Optoelectronic devices, laser and optical benches, scientific instruments, electronics and other products are made of Invar.
Q: What is the minimum size Invar part that is still affordable and has a fast lead time?
A: .08 x .08 x .08" is a good lower limit for Invar parts. Items smaller than that may require extra development time
and tooling expense.
Q: What other items are made of Invar?
A: Here are some uses for Invar:
Electron gun components
Metrology devices
Echo boxes and filters for mobile phones
Dimensionally stable instruments and optical devices
Positioning devices
Bimetal thermostats
High-tech molds
LNG tanks
LNG pipelines
Shielding for magnetic fields
Transformers
Scientific instruments
Circuit breakers
Temperature control devices
Clock balance wheels
Pendulum clocks
Condenser blades
Radar and microwave cavity resonators
Electronic housings
Seals
Spacers
Frames
High voltage power lines
CRT
Shadow masks
Deflection clips
Q: What are some of the physical properties of Invar?
A: See the Invar information page.
Q: What is the emissivity of blackbody coated Mo sheet?
A: For the temperature range of 850-1350 deg. C, the emissivity of blackbody coated
Mo sheet is fairly constant staying in the range of 0.85-0.9 over the entire temperature range of 850-1350 deg. C.
Q: What is the emissivity of uncoated Mo sheet?
A: Figure 67 shows the relationship between temperature and Mo sheet emissivity.
Q: I have a drawing that has a material callout of Crocar. Is that a metal? What is Crocar?
A: Figure 68 shows that Crocar is a metal and the it also shows the composition.
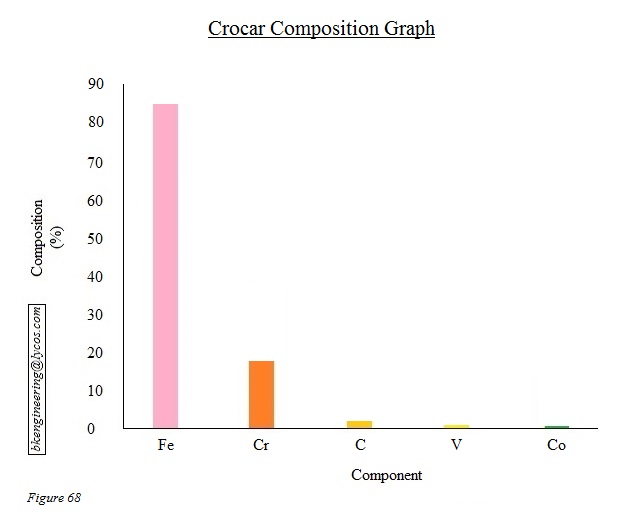
Q: Some of the FAQs discuss ultimate strength but the units have been omitted. What are the standard units for ultimate strength on the FHE FAQ's and figures?
A: When discussing material ultimate strengths on the FHE website, units are always given in thousands of lbs. per square inch.
Q: Is Special defirust rustless iron a particulary soft material and what is the composition?
A: Special defirust rustless iron is almost twice as strong as wrought iron and ingot iron. By the way, wrought iron and Armco ingot iron with a
ultimate strength of 80000 lbs./sq. in. vs. 48 and 48 lbs./sq. in. respectively.
Q: I see some abbreviations such as Ambrac A?
A: There are some abbreviations used in the FAQ and figures. Here is an explanation:
A - Annealed
C- Cold worked
AC - Annealed and cold worked
H - Hardened
HR - Hot rolled
Q: Is there any difference between Stainless B and Sterling Stainless Steel B?
A: Yes, there is a difference, the two materials are not identical. S.B. has more iron and Mn compared to S.S.S.B. S.S.S.B. contains no manganese:
Component |
Stainless B |
Sterling Stainless Steel B |
Fe |
82.8% |
82.5% |
Cr |
16.5% | 16.5% |
C |
0.65% | 0.65% |
Mn |
0.35% | 0.0% |
Q: What is Sweetaloy 16?
A: Sweetaloy 16 is an iron alloy with the following properties:
Specific Gravity
7.83 |
Melting Point
1495 deg C |
Thermal Expansion
11.0 x 10^-6 |
Ultimate Strength
75 thous. lbs./sq. in. |
Q: What is SA2.5?
A: SA2.5 is a visual cleanliness standard.
Q: What is SA3?
A: SA3 is similar to SA2.5 but it calls for better cleaning standards. SA3 is superior to SA2.5.
Q: Does SA stand for "standard abrasive" or "sand abrasive"?
A: SA stands for Sweden Airblast. According to some sources, SA can mean "standard abrasive" or "sand abrasive" as well.
Q: In the SAx standards, what does ST stand for?
A: ST stands for Sweden Tool.
Q: What is ISO 8501?
A: ISO 8501 is a cleaning specification.
Q: What is ISO 8503? Is that a cleaning specification?
A: ISO 8503 is a surface roughness specification.
Q: What is M.T.T.F.?
A: M.T.T.F. is mean time to failure which can be calculated after experimental test data is collected.
Q: Several of F.H.'s charts and reference materials refer to thermal conductivity and data is given. Please explain in greater detail the basis of the data.
A: On our website, thermal conductivity is most often given in terms of g-cal./(sec)(sq. cm.)(deg C/cm). That is the discrete amount of heat (in gram calories) transmitted per second thru a plate of material one (1) cm. thk. and one (1) sq. cm. in area with a temp. difference of 1 deg C between the two sides of the plate.
Q: What about the composition of Sweetaloys other than Sweetaloy 16?
A: COMING!!
Q: I have more questions. What do I do?
A: Text your questions to (408) 475-4551 or (209) 425-1555. You may include illustrations and photographs!! If you prefer email, contact featherholloweng@gmail.com. Calls are also accepted.
Last Update: 10 MAY 2016
|